WHITE PAPER
The Real Dangers of Impact Gun Noise and Vibration Exposure
How transportation maintenance, repair, and operations facilities can protect workers from damage caused by traditional impact guns
The Real Dangers of Impact Gun Noise and Vibration Exposure
How transportation maintenance, repair, and operations facilities can protect workers from damage caused by traditional impact guns
Machine shops and garages are busy places, and you have to be careful where you step. But even the most careful and safety-minded workers are not safe from exposure to noise and vibration. An experienced mechanic, or anyone else working with power tools on a daily basis, can tell you exactly what happens after you’ve been on the job for a while. Numb or white fingers (hand-arm vibration syndrome), elbow pain, carpal tunnel, constant ringing in your ears (tinnitus), hearing loss—all these symptoms are common side effects of repeated and prolonged exposure to noise and vibration from the tools you use every day. Everyone knows that taking proper care of your tools is important, but are you taking proper care of yourself?Who is most at risk?
Anyone who works with power tools is at risk, but especially the 16 million people—or about 13% of the U.S. workforce—employed in manufacturing, including transportation maintenance, repair and operations workers, as defined by the U.S. Bureau of Labor Statistics.
“Occupational hearing loss is the most commonly recorded occupational illness in manufacturing (17,700 cases out of 59,100 cases), accounting for 1 in 9 recordable illnesses. More than 72% of these occur among workers in Manufacturing,” states a report1 by the Centers for Disease Control and Prevention (CDC). “These numbers are particularly disturbing considering that a person’s hearing loss must be determined to be work-related and the hearing loss must be severe enough that the worker has become hearing impaired, in order to be OSHA-recordable. Many more workers would have measurable occupational hearing loss but would not yet have become hearing impaired.” The report goes on to warn, “The rate of hearing loss growth is greatest during the first 10 years of exposure. This means hearing loss prevention is especially important for new workers. However, with continued exposure, the hearing loss spreads into those frequencies most needed to understand speech. This means that preventing occupational hearing loss is also important for workers in their mid and late careers.”
Vibration-related illnesses affecting workers are not new. In fact, some later-stage symptoms, like loss of hearing and “white finger,” have been known since the turn of 20th century, but employers tended to ignore them as just part of the job. Medical evidence and research in support of vibration-protection have been growing for decades. Governments are taking notice and employers are being compelled to face these issues.
Unlike hearing loss, vibration damage can be reversed with proper treatment, but better yet, it can and should be prevented with proper protection. Hand-arm vibration syndrome (HAVS) is the most common set of symptoms that result from using any kind of vibrating tool—from a jackhammer to a dental drill. Longer exposure can increase the risk of developing symptoms. The underlying cause of HAVS is diminished blood circulation to the extremities (specifically fingers). As a result, people who work in cold or damp environments and people who smoke are at an even greater risk of developing HAVS.
An over-torqued bolt can bring the whole machine to a grinding halt.
Metal and alloy bolts are meant to stretch. If a bolt is torqued to engineering spec, a small amount of stretch is normal and won’t cause any future problems. Small stretch doesn’t change the physical properties of the bolt and allows it to get back to its original shape for re-torquing. On the other hand, an over-torqued bolt is stretched so much that its physical properties are changed to the point of compromising its strength and durability. An over-torqued bolt is likely to crack, shear, come loose or break off, and cause major equipment damage or even human injury.
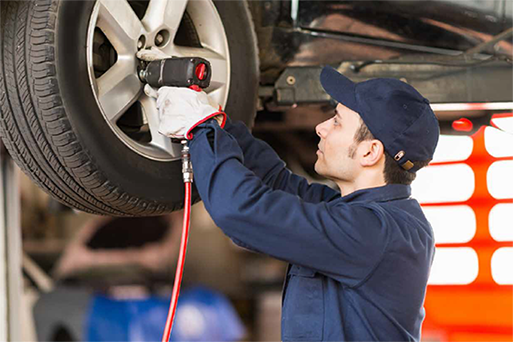
Time to reach 100% noise dose | Exposure level per NIOSH recommended exposure limits |
---|---|
8 hours | 85 dB(A) |
4 hours | 88 dB(A) |
2 hours | 91 dB(A) |
60 minutes | 94 dB(A) |
30 minutes | 97 dB(A) |
15 minutes | 100 dB(A) |
Personal Safety vs. Medical Bills
Unfortunately, not all employers are vigilant against noise and vibration hazards and not many workers are even aware of the dangers before symptoms begin. Vibration damage is not as immediate or dramatic as losing a finger—exposure builds over time. The same is true for hearing loss. Sure, it can seem like a hassle to wear hearing protection in a noisy shop or garage, but hearing loss happens slowly and many workers may not even notice it until it’s too late. While hearing loss is preventable, it is not reversible.
Don’t wait until the pain gets so bad that you need medication or surgery just to keep doing your job. Your body parts are more important than the mechanical ones you’re working on and it’s up to you to protect them.
Correct protective equipment for your hands, feet, eyes, and ears can help dampen the harmful effects, even if not eliminating them altogether. Using better tools—and knowing how to use them to minimize health hazards—can provide a much more effective solution.

Are you safe?
How can you tell whether the noise or level of vibration in your everyday tools is dangerous? Some U.S. manufacturers list tool noise and vibration levels of their products, but it’s not a requirement—yet. And data alone won’t be helpful if you don’t have a frame of reference.
For example, a typical decibel (dB) level (volume) of an impact gun is up to 100dB. It’s not as bad as a hammer drill (nearly 115dB), but it’s significantly over the normal conversation volume of 60dB. It’s important to understand decibel readings—70dB noises are twice as loud as 60dB. Imagine you’re having a conversation in a restaurant (60dB), and suddenly someone starts vacuuming around your table (70dB). Not only would that be annoying, but also you wouldn’t be able to hear what people at your table are saying. Now turn that up to 100 dB (typical impact gun), and the level of noise becomes literally deafening.
Exposure to HAV depends on both the magnitude (intensity) of vibration expressed as acceleration in meters per second squared (m/s2) and the duration of exposure. The daily vibration exposure action value A(8) for a worker carrying out one process or operating one tool can be calculated from magnitude and exposure duration. According to the European Union Manufacturer’s Directive, if a person is exposed to action value over 2.5 m/s2, action should be taken to lessen the exposure. For example, if an impact gun has a declared vibration emission of 16.5 m/s2, using it for longer than 15 minutes at a time, becomes highly hazardous for the worker.
The National Institute for Occupational Safety and Health (NIOSH)—a division of the CDC—offers helpful guidelines on how to estimate safe levels and limit exposure to dangerous noise and vibrations.
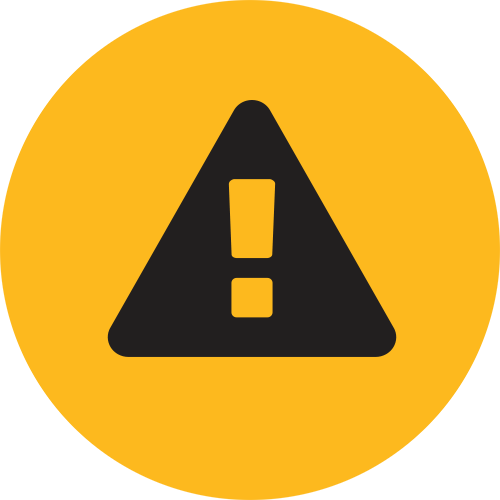
Universal Safety Standards
Another helpful source of power tool safety guidelines is the Manufacturer’s Directives, developed by the E.U. lawmakers. This set of rules requires suppliers to disclose vibration emissions of their tools. However, when reading those, keep in mind that the box refers to brand-new tools and doesn’t take into account everyday wear and tear, which may affect a tool’s vibration emissions.
Some manufacturers are more conscientious than others, and at HYTORC, we hope that companies worldwide can find a way to cooperate in setting reliable (and practical) shared safety standards across industries before international governments require them.

Safety is good business.
Investing in safety makes clear business sense. While the costs of workers’ comp vary by industry, state, and type of injury or illness, insurance claims are just the tip of the expenses iceberg for employers. When calculating safety ROI, employers need to take into account not only the cost of insurance claims, but also expenses and headaches associated with finding another worker to finish the job; any wages paid to the injured employee for absences beyond workers’ comp; costs of schedule disruptions; time spent by employees and specialists who have to handle the claim, etc.
The good news is that safety ROI has been proven again and again by various federal, state, and private-sector programs. Not only do the companies who participate in these programs see a decrease in costs of workers’ compensation and lost worktime, but also they often see increased production and improved employee morale.
Cut the noise with the LION battery-powered torque gun.
By design, impact guns emit a substantial amount of vibrations and noise2 due to the mechanics of how they are powered—a hammering mechanism within the gearbox strikes repeatedly to counter reaction forces. HYTORC recognized this problem and, building on decades of industrial engineering expertise, designed a solution—a cordless torque gun made specifically for smaller bolting applications.
LION vs. Traditional Impact Guns
By design, impact guns emit a substantial amount of vibrations and noise2 due to the mechanics of how they are powered—a hammering mechanism within the gearbox strikes repeatedly to counter reaction forces. HYTORC recognized this problem and, building on decades of industrial engineering expertise, designed a solution—a cordless torque gun made specifically for smaller bolting applications.
The LION is affordable, extremely accurate, and delivers repeatable results. Because of the torque gun’s engineering, there is no hammering mechanism or loud noise emitted during use. In fact, LION Gun’s noise emission is 70-75dB, which is more than 200% lower than some of the upscale products on the market, and well below the OSHA-recommended 85dB level.
No Kickback
Unlike impact guns that can struggle with corroded or damaged nuts and bolts, the LION torque gun provides continuous power with no kickback to break out the nuts that other systems can’t tackle. Breaker bars and slugging wrenches are time consuming and can lead to job-stopping injuries. Impact guns have tremendous vibration and noise and have been banned on many jobsites. The LION uses precision gearing and a simple reaction fixture to give you maximum power, without the noise and vibration.
Ergonomic Design
The LION Gun is built using lightweight but durable materials. The comfort pistol grip and quiet operation ensure that the tool operator is comfortable, even on all-day jobs.
HYTORC makes industrial bolting safer and simpler. Since 1968, the company’s engineers have focused entirely on developing the highest quality industrial bolting systems. From steel mills and mining equipment to refineries, power plants, and wind turbines—HYTORC has developed solutions for every bolting application imaginable.
The LION Battery-Powered Torque Gun brings all of the industrial ingenuity of HYTORC to the commercial marketplace, because safety is equally important whether you are building a NASA spaceship, an Apache helicopter, or a school bus.
Source:
1 “Occupationally-Induced Hearing Loss” DHHS (NIOSH) Publication No. 2010-136
2 The NIOSH Power Tools Database